Our concept
A solution designed for floating wind energy
Eolink is developing a patented pyramidal structure that lines up naturally with the wind direction, like a boat at anchor. The float and turbine are designed simultaneously allowing for a more optimised design.
Eolink’s floating wind turbines are more economical, more efficient and easier to produce.
A pyramid float twice as light
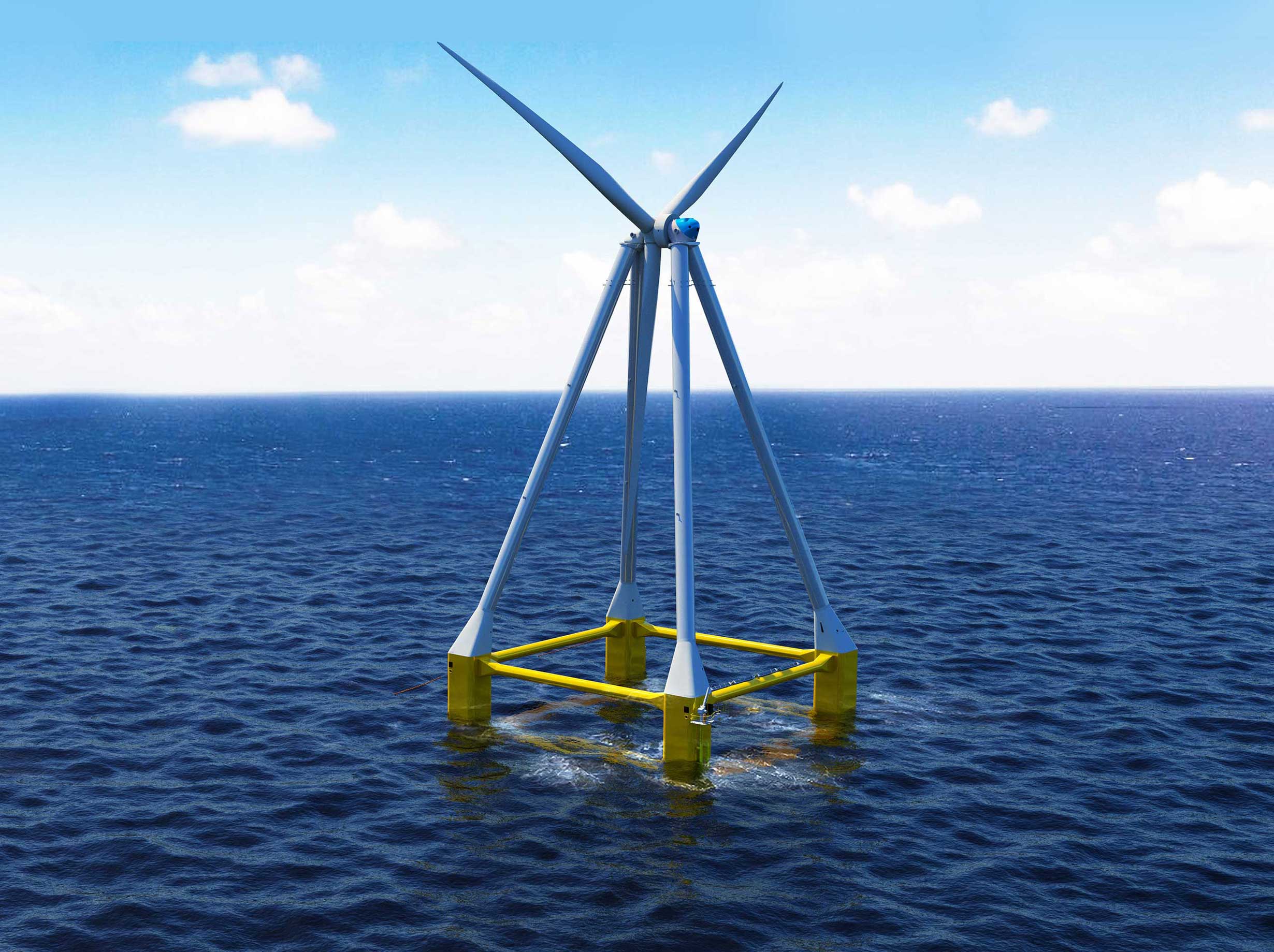
Offshore wind turbines, like ships, are designed to withstand the stresses induced by the marine environment over the long term. For a standard floating structure with a single tower, the forces of the waves and wind generate significant mechanical stresses at the base of the tower due to the large mass at the top of the tower (800 tonnes and more). The structure must therefore be reinforced to withstand these stresses, which are doubled when moving from a fixed to a floating support.
The pyramid structure developed by Eolink distributes these forces efficiently over four columns and is not affected by tilting due to waves or wind.
The pyramid structure developed by Eolink distributes these forces efficiently over four columns and is not affected by tilting due to waves or wind.
This optimised design reduces the mass of steel by 45% compared with the best single-tower floating wind turbine references, allowing the use of 30 mm thick sheet metal compared with the 100 mm usually used with a conventional tower.
With a single tower, the forces double when the turbine is placed on a float rather than fixed to the seabed. This is due to the tilting of the turbine under the action of wind or waves, which generates significant gravitational forces. The pyramid structure is not affected by tilting, so requires less reinforcement. The steel mass of the floater is halved compared to other designs.
Suitable for large turbines >20MW
The competitiveness of offshore wind power is improving with larger turbines. Increasing the power of wind turbine generators is necessary to reduce the levelized cost of floating wind. Indeed, 10 wind turbines of 20 MW produce about as much as 20 wind turbines of 10 MW, but the production and maintenance costs of 10 wind turbines is much lower. With a technology that is particularly well-suited to large turbines, Eolink’s solution
is the perfect answer to this challenge.
Eolink technology increases power by releasing two mechanical constraints.
No vibrations in the masts
The tower of a wind turbine naturally vibrates at a certain frequency (its natural frequency). From 12 MW upwards, conventional wind turbine towers on a floating foundation have a vibration mode that is excited by the rotation of the blades. To overcome this problem, the tower has to be oversized to increase rigidity and weight, which reduces the dimensions of the float.
Because Eolink’s pyramidal structure is much more rigid, the natural vibration frequency (inherent in any structure) is much higher and the vibration problem disappears. This makes it possible to accommodate larger wind turbines.
Longer blades (with no risk of collision with the mast)
The design of the blades must meet two conflicting requirements: the blades must be :
1. Stiff enough not to collide with the tower in high-wind states.
2. Light enough not to suffer from their weight when they rotate.
The pyramidal structure leaves a large space between the blades and the masts. The blades can therefore be more flexible. The weight saved means they can be lengthened.
Designed for mass production
Eolink technology is based on industrial know-how and skills available in the shipbuilding industry, one of the key principles of which is modular manufacture from flat stiffened-steel panels. The panels used are thin and can be easily cut and welded automatically.
This allows Eolink’s technology to be much lighter than other designs currently under development. This has two advantages :
- Minimises the required port/harbour infrastructure improvements and quayside reinforcement, a major challenge for floating wind turbines.
- A shallow draught for easy manoeuvrability of floats in harbours and for towing. Unlocking otherwise unsuitable ports and harbours for floating wind development, and easing the demand on other deepwater quaysides.
Eolink technology uses a modular manufacturing method derived from the shipbuilding industry. Robotic prefabrication of flat stiffened-steel panels enables mass production.
The patented Eolink geometry limits thicknesses to 30 mm, compared with 100 mm for a conventional tower base. Combined with modular block construction, manufacturing is quick and easy.
Lighter and more compact, Eolink technology optimises port space. Its shallow draught makes it easier to manoeuvre floats in harbours and for towing.
Pre-fabricated stiffened steel panels
The panels used are thin and can be easily cut and welded automatically.
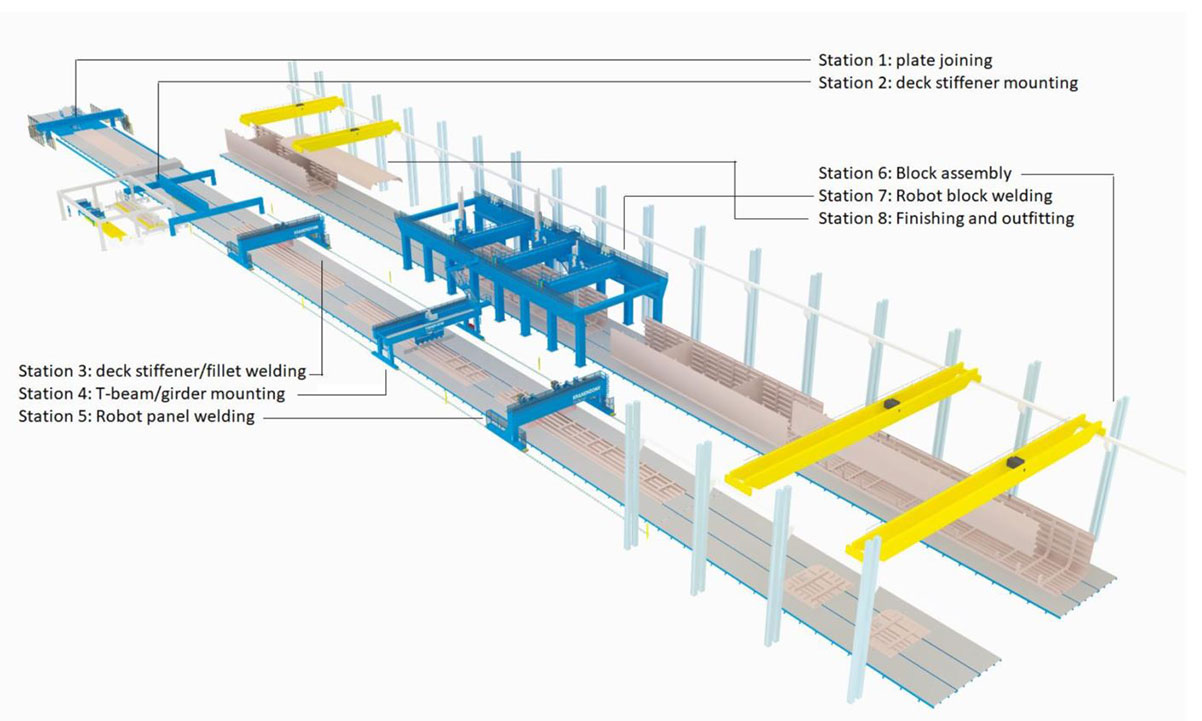
Drawing of a production line of welded steel blocks
Modular assembly
Eolink technology uses a modular manufacturing method derived from the shipbuilding industry.
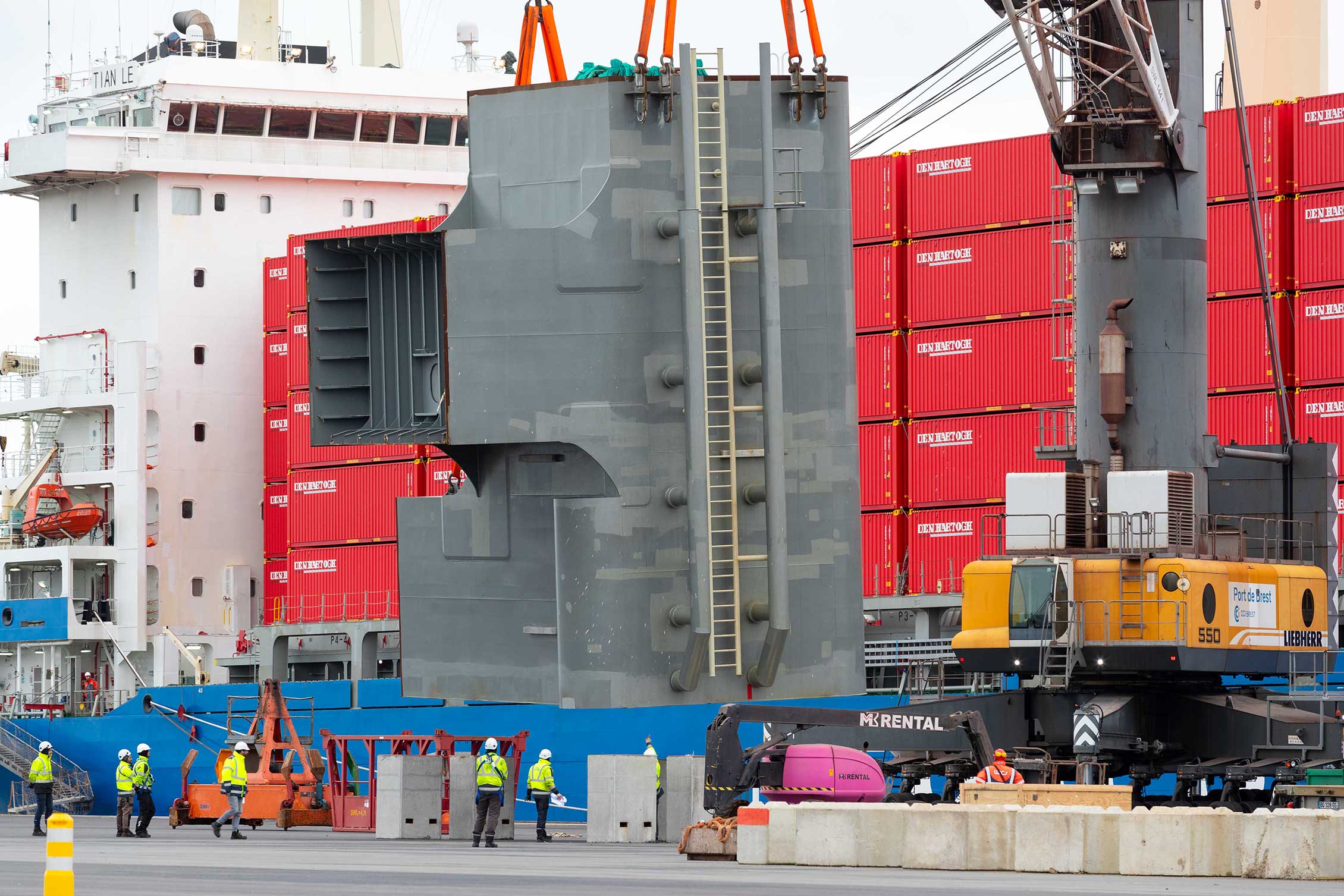
Steel blocks made of stiffened panels (2024)
Optimising port areas
Lighter and more compact, EOLINK technology optimises port space.
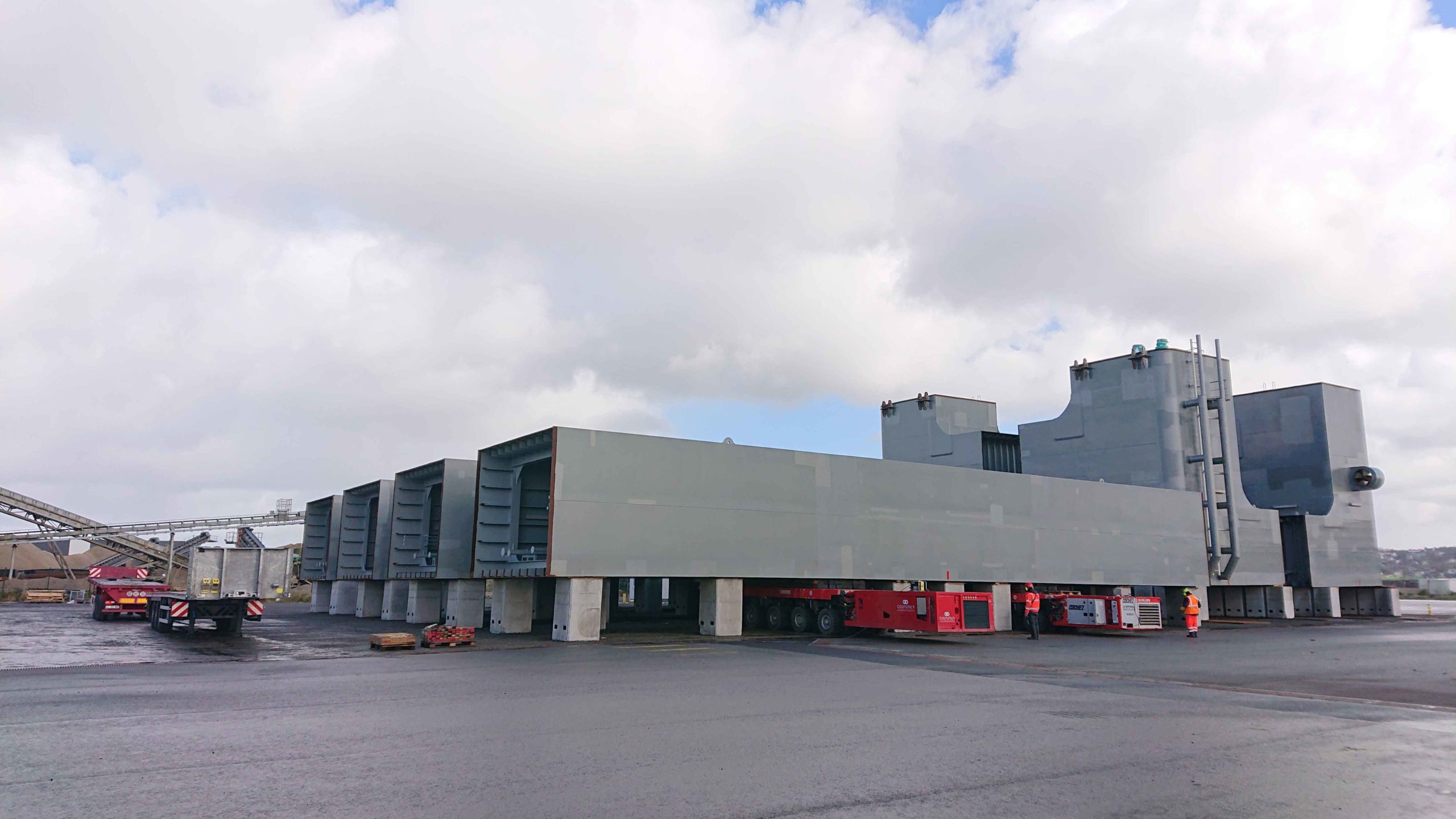
Steel blocks stored in the port of Brest, France (2024)
Ease of operation
Its shallow draught and reduced drag make it easy to manoeuvre in port and tow at sea.
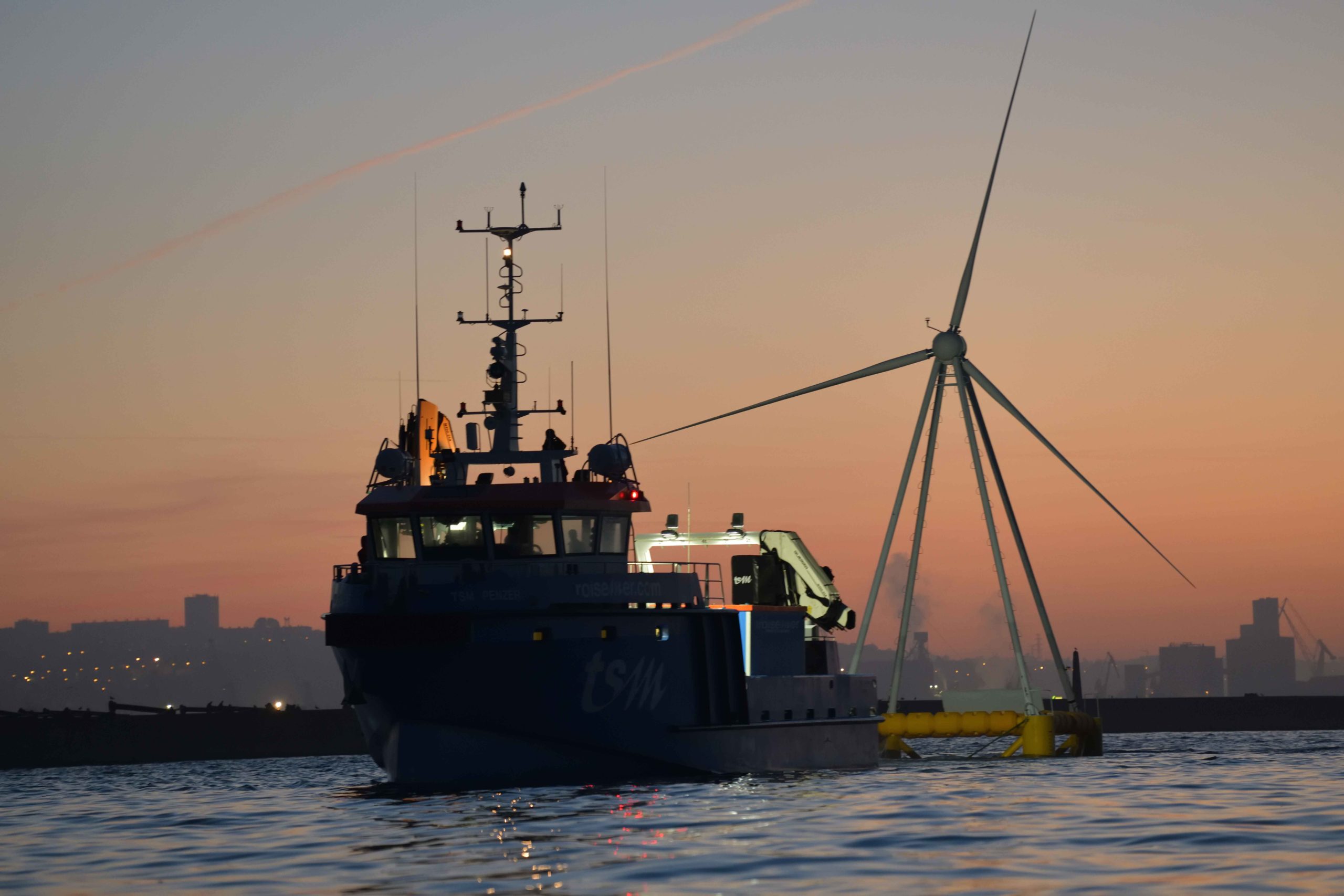
1:10th prototype towing in Brest, France (2018)
Floating wind power
What is floating wind power and what are the advantages ?
Our achievements
See the progress of our projects.